Your Complete Step-by-Step Guide to Waterproofing Successfully
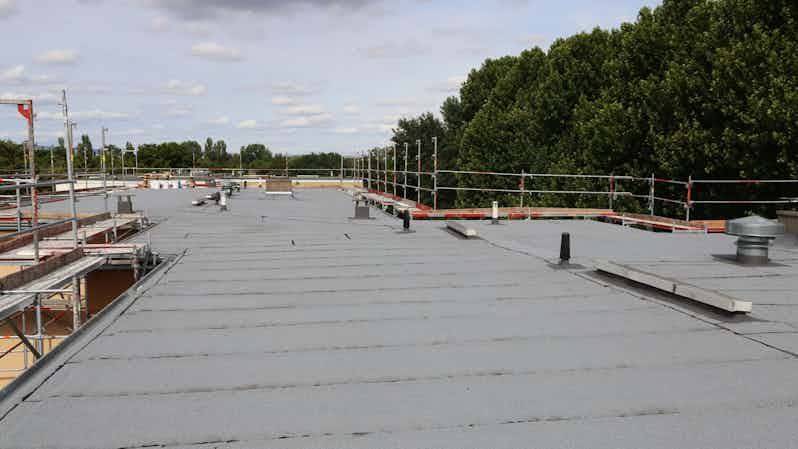
Waterproofing is the silent guardian of your home, an invisible shield that keeps your walls standing, floors dry, and excess moisture or toxic black mould at bay. Yet, in the rush of renovations, especially DIY, it’s often skimped on or slapped together. Unfortunately, there are a lot of cowboy builders out there that also cut corners and customers end up signing up for cracked tiles, rotting frames, and eye-watering repair bills further down the track.
In short, waterproofing is so important in construction. This guide is for both DIY enthusiasts and licensed builders, as well as property developers or facility managers, ensuring building compliance.
We will walk you through waterproofing done right, from why it’s non-negotiable (hello, Australian Standards) to the step-by-step process that saves your sanity (and costly repairs). Let’s dive in.
Step 1 – Planning and Preparation
Remember the cliché, failing to plan is planning to fail? Well, it’s true, especially when it comes to waterproofing efforts. It begins with careful planning and preparation. Rushing this stage can compromise the entire project. Here’s how to start right:
- Identify Critical Areas: Focus on high-risk zones. These are your bathrooms, balconies, basements, and laundry rooms. Each space has unique requirements, such as uneven surfaces, that influence your approach.
- Understand Compliance Standards: Know the standards that apply to the areas that you are waterproofing. Adhering to these standards is essential for compliance and long-term performance.
- Select the Right System: Choose between liquid-applied membranes (ideal for complex shapes) or sheet membranes (great for large, flat surfaces). Consider substrate type, exposure conditions, and manufacturer specifications.
Pro tip: Consult technical datasheets (manufacturer’s detailed product documentation) and, when in doubt, seek professional guidance, especially for structural or high-moisture areas.
Step 2 – Surface Preparation
Even the best liquid waterproofing membrane will fail if applied to a poorly prepared surface. Follow these essential steps to ensure optimal adhesion and performance:
Clean Surface and Dry Completely
Start by scrubbing away all dirt and loose material with a wire brush or vacuum. Don’t rush this step — you’ll want to check for moisture too, because even a little dampness can ruin your waterproofing job.
Repair All Imperfections
For cracks wider than 1mm, fill them with a flexible, waterproof filler designed for your substrate. Seal all penetrations and movement joints with an approved sealant, ensuring complete coverage. Finally, smooth any rough edges or protrusions that could compromise the membrane’s integrity during application.
Prime the Surface Appropriately
Don’t skip the primer, it’s the glue that makes your waterproofing stick! Use the exact primer recommended for your surface (check the product specs), and roll or brush it on evenly—no thick puddles or thin, patchy spots. Then? Walk away. Let it dry fully (yes, even if it looks dry) before touching that membrane.
Pro Tip: “Bond testing” with tape can verify surface readiness before proceeding.
Common Pitfall: Skipping primer to save time leads to 80% of adhesion failures (ASTM data).
Step 3 – Applying the Waterproofing Membrane
With your surface properly prepped, it’s time for the waterproofing membrane. This is the star of the show, a layer that will be your home’s main defence against water intrusion. As such, application technique is everything.
We’ll cover the two membrane waterproofing solutions — liquid membrane and sheet membrane. First, you’ll need the right waterproofing materials.
Tools & Waterproofing Products You’ll Need:
- Notched trowel / squeegee / roller (for sheet membranes).
- Quality brush/roller (for liquid membranes).
- Membrane material (liquid or sheet per your project needs).
- Protective gear (gloves, goggles, and respirator if spraying).
Liquid Membrane Application:
- Stir thoroughly (never shake) to avoid air bubbles.
- Apply first coat with brush in corners/edges first, then roller for large areas.
- Maintain consistent thickness (check manufacturer specs).
- Wait for full curing — check technical sheets — usually 4–24 hours (more on curing below).
- Second coat typically needed — apply perpendicular to first layer.
Sheet Membrane Application Tips
For optimal results with sheet membranes, always dry-fit sections first to plan your layout and minimise material waste. When installing, overlap all seams by manufacturer recommendation, using only the adhesive specified by the membrane manufacturer for a watertight seal.
Be sure to pay particular attention to inside corners and penetrations as these vulnerable areas often require additional reinforcement for a watertight barrier.
Curing and Handling Considerations
Read the manufacturer’s recommended curing times. These typically range between 2–48 hours, depending on the product type and environmental conditions. However, note that recoat timeframes vary significantly between products, so always consult the technical data sheets for precise timing before applying subsequent layers or tiling. Prevent all foot traffic on the membrane during this curing period for obvious reasons.
Pro Tip: Use a wet film gauge to verify liquid membrane thickness as you work.
Common Pitfall: Rushing the curing process leads to compromised performance — patience pays here.
Step 4 – Sealing and Detailing
The best membrane applications have impeccable attention to detail. Take your time because these vulnerable areas demand extra attention:
Corners & Joints (The Leak Hotspots)
High-risk corners and joints can use reinforced protection. You can do this by installing pre-formed corner strips or specialised waterproofing fabric at all internal angles. For liquid membranes, apply an additional brushed coat to these areas prior to the main application.
Important: Maintain flexibility at movement joints. Never bridge them with rigid materials, as this will lead to cracks and failure under stress.
Penetrations: Pipes, Drains, & Niche Edges
Pipe penetrations and drain edges require meticulous detailing. Utilise manufacturer-approved pipe seals or compression rings in combination with the chosen membrane. This is especially vital for shower waste connections.
For drains, always seal behind the flange before final positioning to create a continuous waterproof layer beneath the fitting.
Fixture Integration
Proper integration with fixtures prevents future leaks. Extend the waterproof membrane at least 150mm beyond shower mixer locations, and run protection 100mm up walls behind vanity units. Don’t overlook small penetrations and seal all shower screen bracket screw holes before installation to block potential water pathways.
Pro Technique: “Flood test” shower bases before tiling by plugging drain and filling with water (mark level with pencil and check after 24hrs).
Step 5 – Testing and Inspection
Even perfectly applied membranes require testing. You would be surprised how many improper waterproofing errors are caught before finishes are installed, saving costly repairs. The gold standard of testing is flood testing. Here’s a step-by-step guide:
Flood Testing
- Block all drains securely (use test plugs).
- Fill area with 20mm water depth (mark level on wall).
- Wait 24-48 hours.
- Check for:
– Water level drop (>3mm indicates failure).
– Moisture bleed on ceilings below.
– Damp patches at perimeter junctions.
Adhesion Checks
After curing, test liquid membranes with a press-and-peel tape check (no residue should transfer). For sheet membranes, they must lie flat — no bubbles, wrinkles and resist edge picking. Watch for red flags: discolouration, stress cracks at drains/corners, or musty smells post-installation.
Pro Tip: Document all tests with time stamped photos — insurers and builders require this evidence.
Step 6 – Finishing and Maintenance
Almost there, great job making it this far! Now, let’s lock in that waterproofing success with proper finishing and long-term care.
Tiling Over Waterproofing
Wait until the membrane is fully cured (check step 3) before tiling (if bathroom waterproofing). Remember to use only flexible tile adhesives compatible with your waterproofing system to avoid membrane cracking. Also, protect vulnerable areas (corners, drains) with pre-formed coving or sealing tape during tile installation.
Now, you want your waterproofing to go the distance, so here’s some advice.
Long-Term Waterproofing Maintenance
- Annual Checks: Inspect grout lines/caulking for cracks (reseal immediately).
- Drain Care: Clear shower drains monthly to prevent standing water.
- Leak Alerts: Watch for tiles “hollowing” (sound changes when tapped) or new damp spots.
- Professional Help: Schedule membrane inspections every 5–7 years for high-use areas.
Pro Tip: Keep a note of products used.
Common Waterproofing Mistakes to Avoid
We’ve already touched on these but they’re worth repeating because common mistakes can cost you thousands by not delivering proper waterproofing. Consider this your cheat sheet for what not to do.
Skipping Surface Prep
That “quick wipe” isn’t enough. Grease, dust, or moisture left on surfaces cause 75% of adhesion failures (ABCB data). No membrane bonds properly to a dirty substrate.
Using the Wrong Product
Liquid membranes aren’t universal. Product used in the wrong application – Voided warranty.
Always match the product to:
- Substrate (concrete vs. plywood);
- Location (internal wet area vs. external terrace);
- Traffic (foot traffic requires reinforced membranes).
Rushing Timelines
- Recoat too soon? Layers won’t bond.
- Tile too early? Membrane may mot cure.
- Flood test prematurely? May damage the membrane system.
Pro Tip: Keep a workflow timer on-site (like the Ardex App) to track curing stages.
When to Call a Professional Waterproofing Contractor
Even confident DIYers should consider professional expertise for waterproofing your home. It’s that important, especially for complex or large-scale projects. If there are multi-story balconies or wet areas over 10m², it requires engineered solutions. The same goes for structural cracks or concrete cancer, which affect the structural integrity. The other area where pros are called in is for below-ground waterproofing. This is for jobs like building basements, which have zero margin for error.
Besides the complexities involved, compliance and insurance requirements often tip the scales toward professional waterproofing. Australian Standards specifically require certified installers to maintain valid warranties, and, as you can imagine, insurance providers routinely deny claims for water damage stemming from non-compliant DIY work. Furthermore, in strata and townhouse developments, body corporate regulations nearly always mandate licensed contractors.
At the end of the day, hiring professional waterproofers is worth it for the peace of mind alone.
Your Waterproofing Journey Recap
- Plan (zones, products, compliance).
- Prep (clean, repair, prime).
- Apply (membrane, detailing, curing).
- Test (flood test, adhesion checks).
- Maintain (yearly inspections, prompt repairs).
Need Waterproofing Supplies?
Explore our waterproofing supplies for both DIY-friendly and professional solutions.
FAQs
What is the new Australian standard for waterproofing?
The current Australian Standards are AS 3740 (2021) for wet areas and AS 4654.1 and AS 4654.2 (2021) for external waterproofing, which emphasise proper material selection, effective waterproofing, installation methods, and mandatory testing.
What are the basic principles of waterproofing?
Waterproofing requires a continuous, unbroken barrier — achieved through proper surface prep, compliant materials, detailed sealing at junctions/penetrations, sealing joints, and verification via flood testing.
- Date
- 7.8.2025
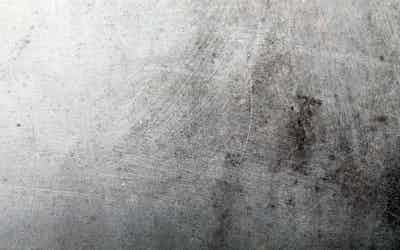