Chemical Resistance Chart
Guide for the chemical resistance of non slip products.
Description
Composites are a combination of fibre reinforcement and a resin matrix. The resin system holds everything together, and transfers mechanical loads through the fibres to the rest of the structure. In addition to binding the composite structure together, it protects from impact, abrasion, corrosion, other environmental factors and rough handling. Resin systems come in a variety of chemical families, with the most commonly used types explained below.
Polyester overview (Orthophthalic, Isophthalic)
Unsaturated polyester resins are the simplest, most economical resin systems that are easiest to prepare and show good performance. They are manufactured by the condensation polymerization of various diols (alcohols) and dibasic acids (e.g. maleic anhydride or fumaric acid) to give esters, a very viscous liquid that is then dissolved in styrene, a reactive monomer. Styrene lowers the viscosity to a level suitable for impregnation or lamination. Generally, polyesters exhibit reasonable thermal stability, chemical resistance, and processability characteristics. Standard Polyesters can be found in most general fibreglass components, but are also widely accepted in power generation and transmission markets, general marine, civil construction, and recreational sectors.
Isophthalic
Often referred to as Iso, it is improved polyester. It has a slightly higher cost, improved strength, thermal stability (55o C) and mild resistance to corrosion conditions. Improved resistance to water permeation has prompted its use as a gel barrier coat in marine applications. Improved chemical resistance has led them to extensive use in moulded gratings, underground petroleum tanks and pultruded structural profiles. They are also used in salty and mildly acidic environments.
Vinyl Ester
Even further improved polyester, it is bisphenol chlorinated, or a combination of polyester and epoxy. Its curing, handling and processing characteristics are those of polyester, and it exhibits higher test results in corrosion temperature resistance and strength and has higher cost. Modifications of the molecule have produced even higher properties. We recommend Vinyl Ester materials for any chemical processing areas, and for structures that require additional strength.
Phenolic
Phenolic resin is a reaction of phenol and formaldehyde. It can be cured via heat and pressure, without the use of catalysts or curing agents. It is one of the oldest thermosetting resins available. Cured phenolic resins are fire resistant without the use of mineral fillers or fire retardant additives. Phenolic composites have excellent high temperature properties, and if properly formulated and cured, they can form carbon to carbon composites with outstanding temperature resistance. Phenolics are also unique in their chemical resistance. Disadvantages of these resins include high curing temperatures and pressures, longer curing times than polyesters, and limited colour range. The use of phenolic resins in composites is growing, primarily due to regulative legislation on flame spread, smoke generation, and smoke toxicity. It is used extensively in automobiles, appliances, electronics, and on off-shore oil and gas platforms.
Product specification sheet
Chemical Resistance Chart product specification sheet opens in a new windowManufacturer
Composite Engineering
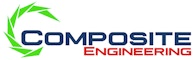
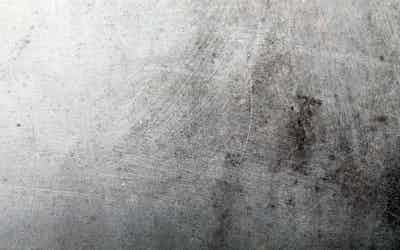